Automated quality control inspection for a manufacturing company
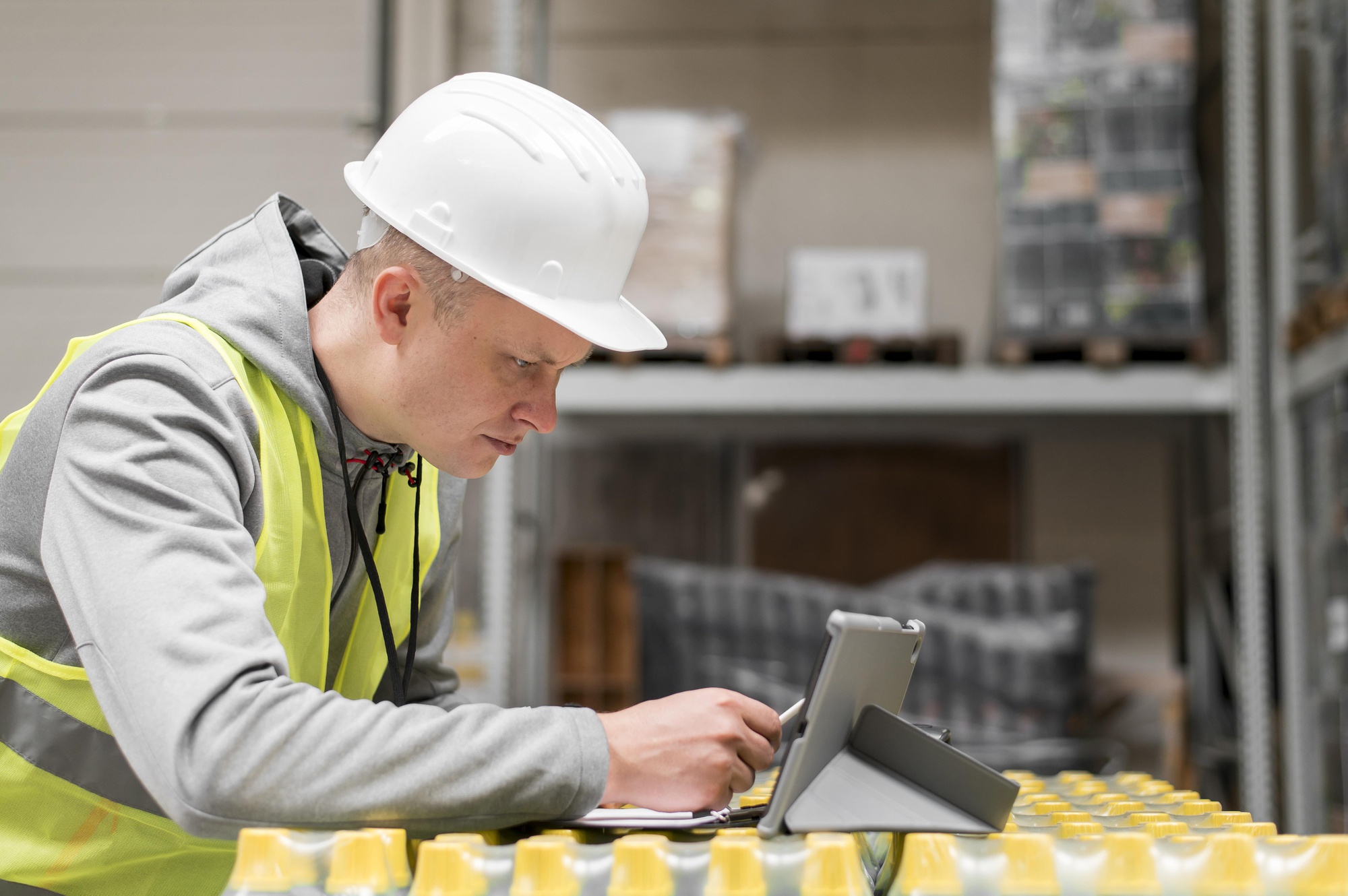
A leading manufacturing company partnered with Fuld & Company to implement an AI-powered automated quality control inspection system. By utilizing neural networks on thermal and X-ray images annotated with defects, we enabled real-time defect detection during the continuous manufacturing process, ensuring high-quality standards and improved operational efficiency.
Key Achievements:
- 92% Defect Detection Accuracy: The AI-powered system achieved a 92% accuracy rate in identifying defects, significantly reducing the chances of faulty products being produced.
- 12% Increase in Operational Efficiency: Real-time defect detection led to a 12% improvement in operational efficiency, minimizing rework and preventing downtime.
How We Did It
- Neural Networks for Real-Time Defect Detection: We applied deep learning algorithms to analyze thermal and X-ray images, training the AI model to recognize patterns associated with defects and flag issues during production.
- Thermal and X-ray Image Analysis: Advanced image processing techniques enabled the system to detect subtle defects that may have been missed by the human eye, ensuring thorough quality checks.
- Continuous Manufacturing Integration: The AI system was seamlessly integrated into the production line, enabling immediate intervention when defects were identified, preventing the manufacturing of faulty products.
- Feedback Loop for Continuous Improvement: Detected defects were logged, feeding data back into the neural network to continuously improve the accuracy of defect detection over time.
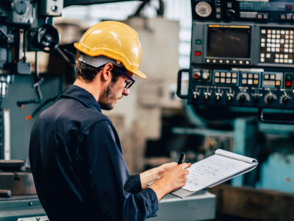