Predictive maintenance for a tire manufacturer: Enhancing productivity and reducing downtime with industry 4.0
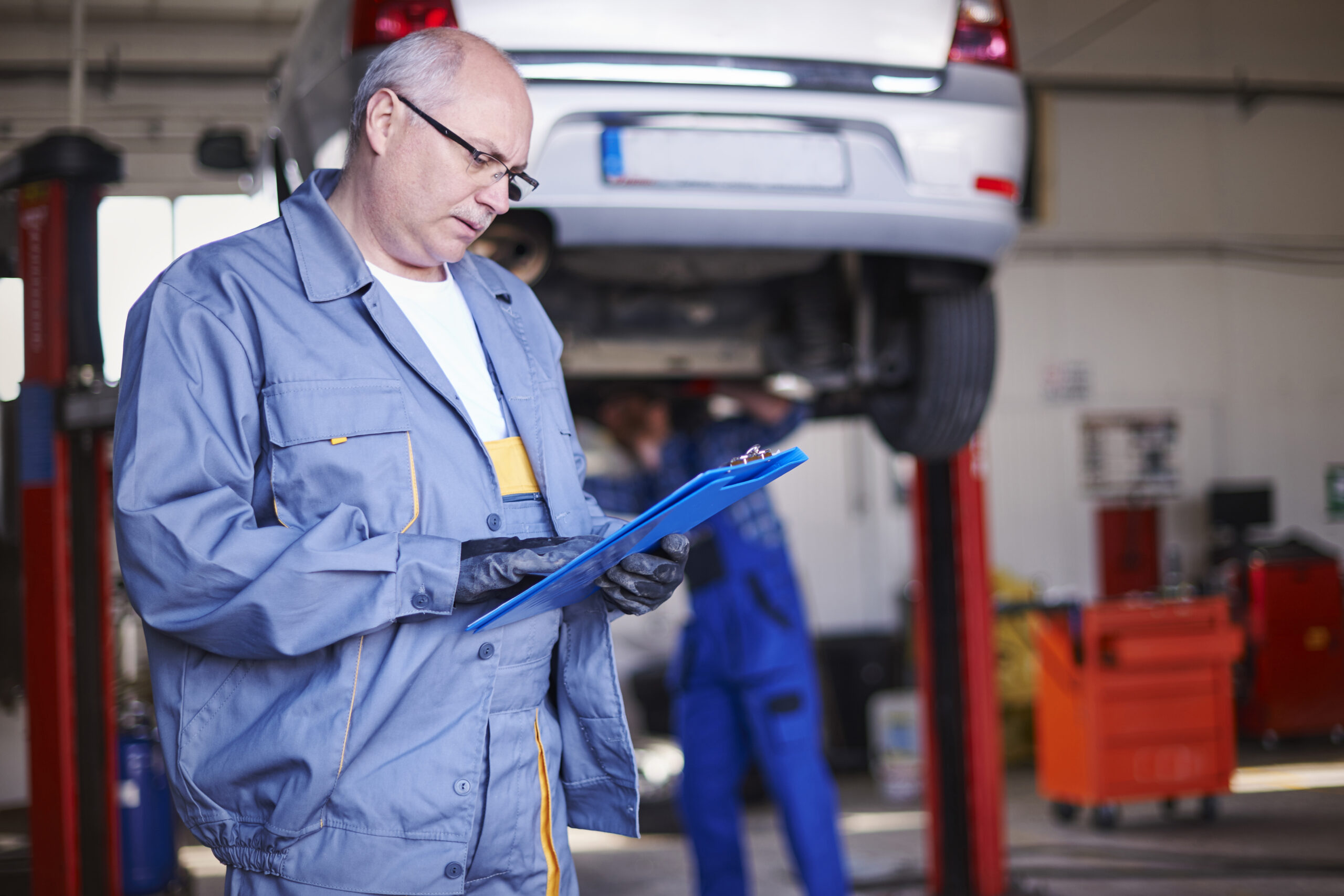
A leading tire manufacturer partnered with Fuld & Company to implement Predictive Maintenance using Industry 4.0 principles. By leveraging advanced data pipelines and predictive analytics, we empowered the manufacturer to monitor and maintain critical assets proactively. This approach minimized costly downtime and boosted productivity across the factory floor.
Key Achievements:
- 15% Reduction in Manufacturing Downtime: By identifying and addressing potential failures early, the manufacturer reduced unplanned downtime by 15%, improving production efficiency.
- 12% Reduction in Maintenance Costs: The shift from a reactive to predictive maintenance approach resulted in a 12% decrease in overall maintenance costs, focusing resources only on equipment showing signs of wear or potential failure.
- Optimized Operational Efficiency: The proactive maintenance system ensured minimal disruption to production schedules, driving a more efficient and cost-effective manufacturing process.
How We Did It
- Predictive Analytics for Asset Health Monitoring: Integrated IoT devices and sensors to monitor critical assets (such as heaters and extruders) and used predictive analytics to detect early failure signs, enabling timely interventions.
- Real-Time Data Pipelines: Developed robust data pipelines for continuous data collection, processing, and analysis, providing actionable insights for quick decision-making.
- Industry 4.0 Integration: Leveraged smart factory technologies and AI-driven insights to detect anomalies and trigger automated maintenance alerts, reducing downtime and maintaining smooth operations.
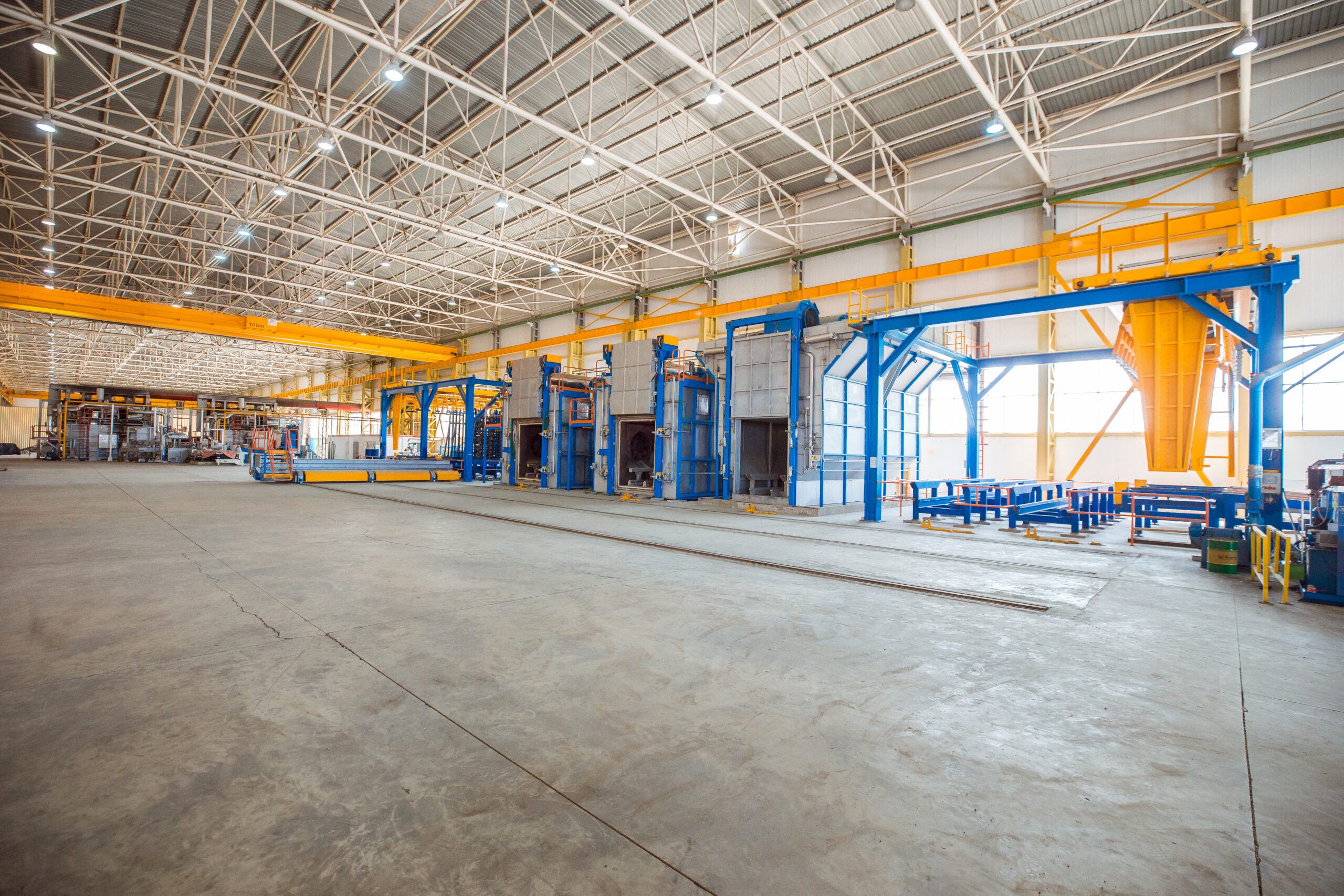